Traceability remains a buzzword in the manufacturing world, and for good reason
|
 |
|
Traceability remains a buzzword in the manufacturing world, and for good reason. Achieving high traceability within an organization essentially means materials or product components are consistently and accurately tracked from initial arrival at a production facility to finished goods being shipped.
|
|
|
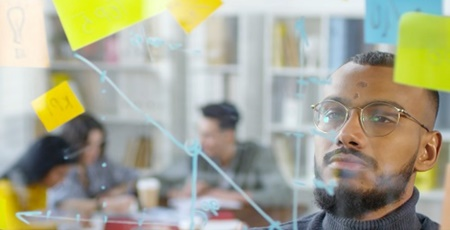 |
How to improve traceability within a manufacturing facility
Traceability is critical in the production process because that process is not perfect. There are times when errors in the process occur or products make their way through it but are not up to standards in terms of quality. In these instances, having the ability to perform a root cause analysis and easily determine when and where errors occurred is crucial. Faster identification means a quicker resolution of personnel, material, or machine issues – saving an organization time and money. More...
|
 |
|
Schaeffler (Singapore) President for Industrial shares 2023 outlook
Uncertainties have been compounding in the recent past, with developing signs of weakness in economic growth and other high-frequency parameters. To provide manufacturing decision-makers in South East Asia with improved insight into global economic conditions in 2023, International Metalworking News for Asia asked thought-leaders in the metalworking industry how their technology can give the industry a positive outlook for the future. More...
|
|
Renishaw brings advanced manufacturing solutions to South East Asia
Manufacturers nowadays are progressively looking to automation in order to propel operational efficiency and overcome skill shortages on the shop floor. To control manufacturing processes on the shop floor, the need for new process control methods, such as gauging systems are increasing. Steve Bell, General Manager of Renishaw ASEAN highlighted the Equator 300 and 500 flexible gauge system, which is suitable for automation requirements. More...
|
|
|
Everything under control at lightning speed
The KR 3 D1200, the latest delta robot model from KUKA, proves itself in pick-and-place of foodstuffs, among other applications, and carries up to 6 kg. With high speed. Although the KR 3 D1200 has a rated payload of 3 kg, it is designed for loads of up to 6 kg. This makes it one of the strongest delta robots on the market. The small footprint with a diameter of 350 millimeters makes ceiling mounting space-saving and efficient. More...
|
|
Turn up: larger, lighter additive parts
GE Aerospace Advanced Technology Munich-led European consortium unveils one of the largest- ever metal 3D-printed aerospace parts and demonstrates significant cost, weight, and time savings. The EU’s European Green Deal sets out the need to reduce transport emissions by 90% by 2050, compared to 1990 levels, with the aviation sector playing its part. Policy actions and industry efforts since 2005 have led to greater fuel efficiency per passenger. More...
|
|
A scalable end-to-end solution for digital twins
Altair launched a comprehensive technology solution for digital twins. This is designed to provide highly interconnected, cross-discipline capabilities that can be deployed at various stages of the product lifecycle. Combining Altair's expertise in simulation, high-performance computing, AI, data analytics and the Internet of Things will enable companies to use Digital Twin technology at every stage of the product lifecycle in the future - from concept to commissioning. More...
|
|
Overcoming inhomogenous strength properties in 3D printing
Every 3D printing process competes with classic manufacturing strategies such as casting or milling in terms of mechanical properties, time factors and cost-effectiveness. It is also in competition with alternative 3D printing technologies. The technological challenge: at present, layer-based 3D build processes of polymers often exhibit inhomogeneous structural properties. More...
|
|
|
|
|
 |
|
|
|